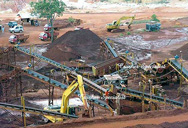
Advances in Sintering and Pellet Technology - MDPI
2022年6月20日 Sintering and pelletization processes are largely influenced by the source of iron ore and the way in which the beneficiation flowsheet is adopted. The beneficiation and agglomeration processes largely depend on the mineralogical characteristics of the ore.
More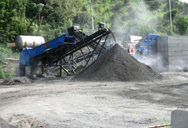
Iron Ore Sinter - an overview ScienceDirect Topics
Sintering is the most economic and widely used agglomeration process to prepare iron ore fines for blast furnace use. Compared with pellets, production of sinter is cheaper, and
More
Sintering: A Step Between Mining Iron Ore and Steelmaking
2019年6月11日 According to the U.S. Environmental Protection Agency, the sintering process converts fine-sized raw materials, including iron
More
Sintering and Pelletizing - Outotec
Our innovative sintering and pelletizing solutions are based on over 60 years’ experience and world-class RD. Outotec Traveling Grate Sintering is suitable for sintering
More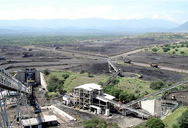
Strengthening Granulating and Sintering Performance of
2023年3月30日 May Concentrate Iron ore, as a refractory iron concentrate, deteriorates the permeability of the sintered layer during the sintering process due to its fine particle
More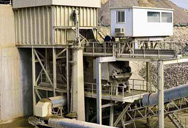
Reduction of Iron Ore Pellets, Sinter, and Lump Ore under
Sinter, lump ore, and iron ore pellets were used in experiments. The composition for all three materials is shown in Table 1. The total iron content (Fe tot) and the oxidation
More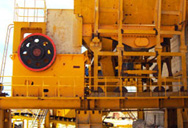
Preparation of Iron Ore Micro-pellets and Their Effect on
2018年6月13日 In hybrid pellet sintering process, iron ore concentrate of relatively finer size is first converted into micro-pellets and these micro-pellets are used in place of
More
New Process of Pellets-Metallized Sintering Process
2014年11月20日 The typical composition ranges of exhaust gases from common iron ore sintering are reported to be in the range of 2 to 16 pct CO 2, 1 to 3 pct CO, and 8 to 15
More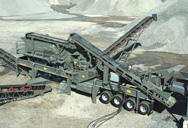
Reduction of Iron Ore Pellets, Si... preview related info Mendeley
Herein, the reducibility of the iron ore pellet, sinter, and lump ore in the BF shaft are focused on. The experiments are conducted isothermally with a blast furnace simulator
More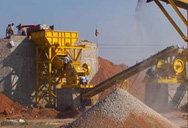
A comparative study of pellets, sinter and mixed ferrous
Commercially supplied iron ore pellets and sinter of size range 10–13 mm are utilised in the present study. Comparable to the utilisation in the industrial blast furnace, two types
More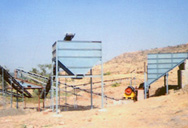
Novel sintering indexes to evaluate and correlate the crystal ...
2020年2月15日 Introduction. Iron ore pellets are important raw materials for blast furnaces and are essentially spheres with a diameter of 8–16 mm [1]. The pelletization process combines the mixing of the raw materials, such as ultra-fine-sized ore, dolomite, and bentonite, forming the pellets, oxidizing and roasting to achieve required chemical
More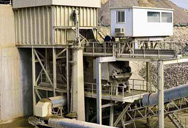
A comparative study of pellets, sinter and mixed ferrous burden ...
Commercially supplied iron ore pellets and sinter of size range 10–13 mm are utilised in the present study. Comparable to the utilisation in the industrial blast furnace, two types of olivine fluxed pellets (types 1 and 2) and one type of iron ore sinter are mixed in 40:20:40 ratio to form a ferrous raw material bed.
More
Improving properties of fluxed iron ore pellets with high-silica by ...
2021年9月20日 Iron ore pellets have been proved to possess preferable size and shape, mechanical strength and metallurgical properties, compared with the sinters during the blast furnace ironmaking process [ 4, 5 ]. Under the background of green development, it is an inevitable trend to increase the proportion of pellets in blast furnace burden.
More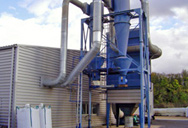
Strengthening Granulating and Sintering Performance of Refractory Iron
2023年3月30日 May Concentrate Iron ore, as a refractory iron concentrate, deteriorates the permeability of the sintered layer during the sintering process due to its fine particle size and poor granulating performance. Therefore, it cannot be widely used in iron ore sintering. In this study, the strengthening granulation of May Concentrate Iron ore using pre
More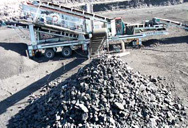
Quantitative XRD analysis and evaluation of iron ore, sinter, and pellets
2022年1月1日 Powder X-ray diffraction (XRD) is increasingly being used for the characterization of iron ore, sinter, and pellets thanks to the continuing developments in its instrumentation and software that enabled scientists and engineers to quickly analyze and quantify minerals and phases in often nonhomogeneous materials.
More
New Process of Pellets-Metallized Sintering Process
2014年11月20日 The typical composition ranges of exhaust gases from common iron ore sintering are reported to be in the range of 2 to 16 pct CO 2, 1 to 3 pct CO, and 8 to 15 pct O 2. As seen in Figure 3, during the metallized sintering process, the contents of CO 2, CO, and O 2 in the exhausted gas are 12 to 15, 10 to 13, and 2 to 5 pct, respectively. The ...
More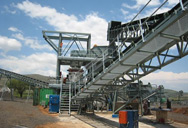
Iron Ore Pelletizing Process: An Overview IntechOpen
2018年7月11日 The iron ore pelletizing process consists of three main steps: Pelletizing feed preparation and mixing: the raw material (iron ore concentrate, additives—anthracite, dolomite—and binders are prepared
More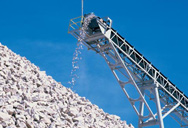
Study on Sintering and Reduction of Ultra-Fines
2015年1月6日 Recently a special attention is paid on the utilization of ultra-fine iron ore (-0.2 mm) in the form of micro-or mini-pellets in the sintering process. In the current study the ultra-fines iron ...
More
Our Products - Iron Ore Company of Canada
With a high-quality iron ore reserve and a long mine life, IOC is a global leader in the high quality iron ore sector, producing premium DR and BF pellets and sinter feed. IOC’s pellets and concentrate are high grade products with world leading low alumina and ultra-low phosphorus, beneficial to the iron steel industry.
More
Reduction of Iron Ore Pellets, Si... preview related info Mendeley
Herein, the reducibility of the iron ore pellet, sinter, and lump ore in the BF shaft are focused on. The experiments are conducted isothermally with a blast furnace simulator (BFS) high-temperature furnace at four different temperatures (700, 800, 900, and 1000 °C) for 300 min. The experimental atmosphere consists of CO, CO2, H2, H2O, and N2 ...
More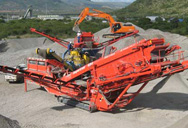
Working Animation Of Iron Ore Pellet Plant - degraeflinsen
Iron Ore Pellets Production Flow Chart. Process Flow Diagram Of Pellet Plant Binq Mining. Iron Ore Beneficiation Process Flow Chart For Processing Plant . ... Sinter plants agglomerate iron ore fines (dust) with other fine materials at high temperature, to create a product that can be used in a blast final product, a sinter, is a small ...
More
Outotec to further reduce its metals presence
2023年3月29日 The Ferrous Heat Transfer unit potentially includes its sintering and pelletizing technology, including systems for iron ore pellet production. In late 2021, Outotec announced it had agreed to sell its Metal Recycling business line to an affiliate of Mimir, an investment company based in Stockholm.
More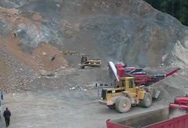
Iron Ore Agglomeration Technologies IntechOpen
2017年12月20日 The formation of liquid phases, which agglomerate the iron ore, in pellets is achieved by an external source of energy (fuel, natural gas ... Fernández-González D, Ruiz-Bustinza I, Mochón J, González-Gasca C, Verdeja LF. Iron ore sintering: Raw materials and granulation. Mineral Processing and Extractive Metallurgy Review.
More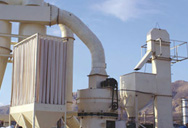
From mine to port - LKAB
The iron ore pellets are then dried and preheated before finally being heated at 1,250°C to a point where the iron ore particles partially fuse together. Before delivery, the pellets are cooled down. ... An iron ore sinter is a type of agglomorate iron ore, just like pellets. Sinter is a piece of iron ore that has an irregular shape, and is ...
More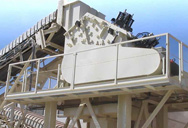
Novel sintering indexes to evaluate and correlate the crystal ...
2020年2月15日 According to the literature research, only three papers have mentioned the quantitative characterization of the sintering degree of pellets. Heidy et al. [25] presented a method to measure the sintering degree of iron ore pellets via the image processing method by an optical microscope.
More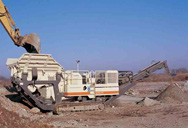
Review of computational fluid dynamics modeling of iron sintering ...
2022年9月1日 The sintering process not only improves the quality of steel products, but also releases CO and CO 2 gases, evaporates moisture, and improves the reducibility of iron ore to ensure smooth operation of the blast furnace. These factors are related with variables such as temperature and flux, so optimization is essential.
More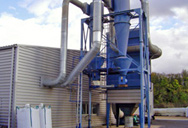
Strengthening Granulating and Sintering Performance of Refractory Iron
2023年3月30日 May Concentrate Iron ore, as a refractory iron concentrate, deteriorates the permeability of the sintered layer during the sintering process due to its fine particle size and poor granulating performance. Therefore, it cannot be widely used in iron ore sintering. In this study, the strengthening granulation of May Concentrate Iron ore using pre
More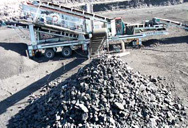
Quantitative XRD analysis and evaluation of iron ore, sinter, and pellets
2022年1月1日 Powder X-ray diffraction (XRD) is increasingly being used for the characterization of iron ore, sinter, and pellets thanks to the continuing developments in its instrumentation and software that enabled scientists and engineers to quickly analyze and quantify minerals and phases in often nonhomogeneous materials.
More
New Process of Pellets-Metallized Sintering Process
2014年11月20日 The typical composition ranges of exhaust gases from common iron ore sintering are reported to be in the range of 2 to 16 pct CO 2, 1 to 3 pct CO, and 8 to 15 pct O 2. As seen in Figure 3, during the metallized sintering process, the contents of CO 2, CO, and O 2 in the exhausted gas are 12 to 15, 10 to 13, and 2 to 5 pct, respectively. The ...
More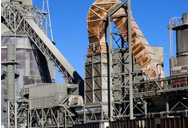
Iron Ore Agglomeration Technologies IntechOpen
2017年12月20日 The formation of liquid phases, which agglomerate the iron ore, in pellets is achieved by an external source of energy (fuel, natural gas ... Fernández-González D, Ruiz-Bustinza I, Mochón J, González
More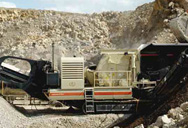
Study on Sintering and Reduction of Ultra-Fines
2015年1月6日 Recently a special attention is paid on the utilization of ultra-fine iron ore (-0.2 mm) in the form of micro-or mini-pellets in the sintering process. In the current study the ultra-fines...
More
Our Products - Iron Ore Company of Canada
With a high-quality iron ore reserve and a long mine life, IOC is a global leader in the high quality iron ore sector, producing premium DR and BF pellets and sinter feed. IOC’s pellets and concentrate are high grade products with world leading low alumina and ultra-low phosphorus, beneficial to the iron steel industry.
More
Reduction of Iron Ore Pellets, Si... preview related info Mendeley
Herein, the reducibility of the iron ore pellet, sinter, and lump ore in the BF shaft are focused on. The experiments are conducted isothermally with a blast furnace simulator (BFS) high-temperature furnace at four different temperatures (700, 800, 900, and 1000 °C) for 300 min. The experimental atmosphere consists of CO, CO2, H2, H2O, and N2 ...
More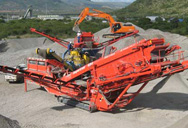
Working Animation Of Iron Ore Pellet Plant - degraeflinsen
Iron Ore Pellets Production Flow Chart. Process Flow Diagram Of Pellet Plant Binq Mining. Iron Ore Beneficiation Process Flow Chart For Processing Plant . ... Sinter plants agglomerate iron ore fines (dust) with other fine materials at high temperature, to create a product that can be used in a blast final product, a sinter, is a small ...
More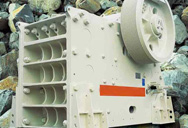
Why green iron ore may be the next big wave
2023年1月9日 This expected rise in demand for direct-charge materials is clear, with major Brazilian miner Vale looking to ramp up its production of pellet and briquette to around 22% of its total production, or about 100
More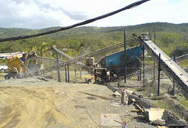
From mine to port - LKAB
Pelletisation: In large rotating drums, the slurry are rolled into small balls called pellets. The iron ore pellets are then dried and preheated before finally being heated at 1,250°C to a point where the iron ore particles partially fuse together. Before delivery, the
More
Outotec to further reduce its metals presence
2023年3月29日 The Ferrous Heat Transfer unit potentially includes its sintering and pelletizing technology, including systems for iron ore pellet production. In late 2021, Outotec announced it had agreed to sell its Metal Recycling business line to an affiliate of Mimir, an investment company based in Stockholm.
More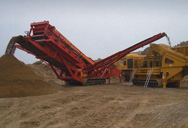
Minerals Free Full-Text Quantitative Investigation of MgO,
2022年1月6日 Secondary hematite (SH) is a serious factor resulting in reduction degradation of iron ore sinter in a blast furnace; however, until now, a quantitative study for SH formation had not been reported. In this work, the effects of gangue composition, including MgO, Al2O3 and SiO2, on the solid-state formation in the sintering process of
More