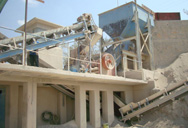
Pelletization - Outotec
Pelletization is the process of transforming iron ore fines into spherical pellets through agglomeration and induration. These pellets are then used as feed to a blast furnace or
More
Flowchart in the pelletizing process Download Scientific
One of the first successful applications of the technology has been in iron ore pressing prior to pelletization. Piston-and-die tests can provide good insights on the material response
More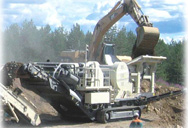
m/sbm ore pelletisation process flow chart.md at main
Contribute to legaojm/m development by creating an account on GitHub.
More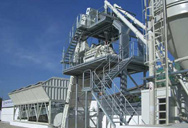
Chart For Processing Iron - degraeflinsen
Process flow chart of iron ore pelletizing industry. Pellet plant is facilitated with additives grinding unit as the process of pelletization requires binder and additives. Bentonite is
More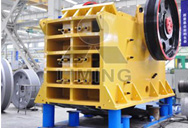
Iron Ore Pelletization: Part I. Fundamentals - Taylor Francis
2021年3月15日 The contributions of binders such as bentonite, starch, cements, dispersants, fluxes, and other additives which have been used in pellets are discussed
More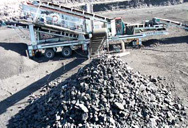
Iron Ore Pellets and Pelletization Process – IspatGuru
2014年11月26日 Pelletizing of iron ore was started in the 1950s to facilitate the utilization of finely ground iron ore concentrates in steel production. For the pelletizing of iron ore
More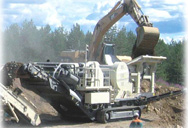
Iron Ore Pelletization - FEECO International Inc.
The mixing stage thoroughly mixes the iron ore, binder, and any additives in order to provide the pelletizer with a uniform feedstock. Pelletizing Material exiting the mixer is
More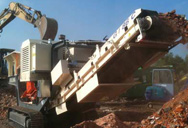
Iron ore pelletizing - Outotec
Our iron ore pelletizing systems combine the best features of both technologies to provide the most modern plant and to produce pellets at the lowest cost and highest quality. Pellet plants sized from 1.2MTPA to
More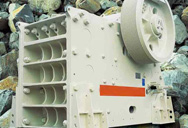
Iron Ore Pelletization: Part I. Fundamentals - Taylor Francis
2021年3月15日 The contributions of binders such as bentonite, starch, cements, dispersants, fluxes, and other additives which have been used in pellets are discussed with particular emphasis on how these effects paint a coherent picture of the pelletization process as whole.
More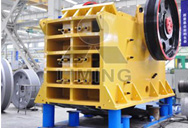
KOBELCO Pelletizing Process
iron briquettes. Sintered ore is made by partially melting and sintering coarse iron ore 1 to 3mm in size into products having a size of 15 to 30mm. The sintering process uses the combustion heat of coke breeze (fuel). Pellets are made from iron ore that is finer than that used for sintered ore. The ore fine is formed
More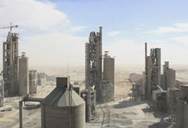
New Paradigms for Iron Ore Pelletization SpringerLink
2018年8月19日 Thus, in iron ore pelletization , class C and class F fly-ashes may both undergo pozzolanic reactions. Fly-ashes which do not meet ASTM C618 may still be useful as pellet binders, so long as they are pozzolanic. These fly-ashes are generally disposed of in landfill as solid waste, as they are unsuitable for use in construction materials or cement.
More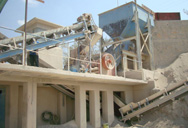
(PDF) Iron ore pelletization - ResearchGate
2015年12月31日 Iron ore pelletization. A brief introduction to recent developments in iron ore pelletizing is provided in this chapter, including the world output of fired pellets, pellet production processes ...
More
Process flow chart of preparation of pellets
Lime was used as additive as well as fluxing agent for making iron ore pellets. The effect of additives on different properties of pellets was studied. The findings show that on increasing the...
More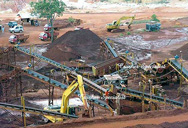
Iron Ore Pellets and Pelletization Process – IspatGuru
2014年11月26日 Pelletizing of iron ore was started in the 1950s to facilitate the utilization of finely ground iron ore concentrates in steel production. For the pelletizing of iron ore there are two main types of processes namely, the straight travelling grate (STG) process and the grate kiln (GK) process.
More
m/sbm ore pelletisation process flow chart.md at main legaojm/m
Contribute to legaojm/m development by creating an account on GitHub.
More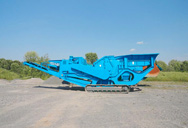
SINTERING AND PELLETISATION OF INDIAN IRON ORES
High grade iron ore less than 10% of the total reserves. ROM iron ore with Fe less than 58 – 60% discarded as waste. After beneficiation iron ore availability can improve by about 50%. Steel community and the country demand technological solutions for utilising low grade ores. The technology task that would be imperative: 1.
More
Chart For Processing Iron - degraeflinsen
Process flow chart of iron ore pelletizing industry. Pellet plant is facilitated with additives grinding unit as the process of pelletization requires binder and additives. Bentonite is used as a binder for proper balling of the filter cake particles in to spherical shaped balls with certain compression strength. The bentonite is stored and ...
More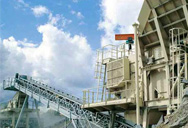
Iron ore pelletization - ScienceDirect
2022年1月1日 Generally, any material being considered for pelletizing should contain at least 70% −44 μm material and have a specific surface area (Blaine index) of >1200 cm 2 /g to ensure good balling characteristics ( Poveromo, 2014; Indian Bureau of Mines, 2011 ).
More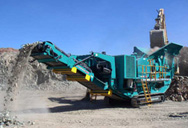
Introduction to Iron ore Pellets and Pelletizing
2013年2月23日 Pelletizing is a process which involves mixing of very finely ground particles of iron ore fines having a size which is less than 200 mesh (0.074 mm) with additives like bentonite and then shaping them into near
More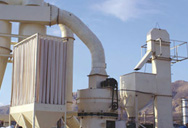
Our Businesses overview – EMIL
The IoBP plant comprises of a 1 MTPA Iron Ore Beneficiation plant and a 1 MTPA Iron Ore Pelletization plant based on first of its kind Circular Pelletization Technology (CPT) EMIL is also a pioneer in manufacturing of world class Noble Ferro Alloys (NFA) and Iron pellets. The Noble Ferro Alloys (NFA) unit is located in Valsad district of ...
More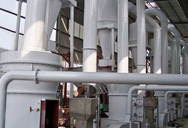
Iron Ore Pelletization: Part III. Organic Binders - Taylor Francis
2022年1月25日 This part reviews the goals of introducing organic binders into iron ore pelletization. Organic binders present a relatively small number of unique binding options but provide an extraordinary amount of flexibility in how to apply them. The key factors that lead into an effective organic binder are good dispersion into the iron ore, the ability ...
More
Iron Ore Pelletizing Diagram - degraeflinsen
pelletizing plant process flow diagram. Iron Ore Pelletizing Process: An Overview IntechOpen. Jul 10, 2017 Figure 2 shows a flowchart of a typical pelletizing plant, highlighting the additive preparation, mixing and pelletizing feed preparation, the balling step, in this case using a disc pelletizer, and the induration step.
More
Analysis of iron ore pellets properties concerning raw material ...
2022年3月1日 The pellets were prepared by blending iron ore fines (64% Fe, 2.25% LOI, and Blaine number = 2975 cm 2 /g) and slimes (52.45% Fe, 5.60% LOI, and Blaine number = 7064 cm 2 /g) generated from the beneficiation plant. The utilization of slimes replaces the external binder addition during pellet making.
More
New Paradigms for Iron Ore Pelletization SpringerLink
2018年8月19日 Essentially all iron ore processed in the United States is pelletized before being reduced to metallic iron . Pelletization ensures a consistent size distribution and simplifies transportation, but requires the addition of binders to ensure pellet strength.
More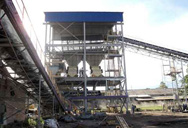
Iron Ore Pelletization - FEECO International Inc.
The mixing stage thoroughly mixes the iron ore, binder, and any additives in order to provide the pelletizer with a uniform feedstock. Pelletizing Material exiting the mixer is continuously fed into the pelletizing device, along with additional liquid binder.
More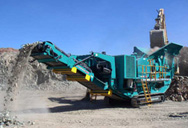
Introduction to Iron ore Pellets and Pelletizing
2013年2月23日 Pelletizing is a process which involves mixing of very finely ground particles of iron ore fines having a size which is less than 200 mesh (0.074 mm) with additives like bentonite and then shaping them into near
More
m/sbm ore pelletisation process flow chart.md at main legaojm/m
Contribute to legaojm/m development by creating an account on GitHub.
More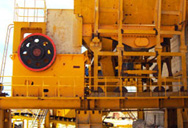
sbm/sbm flow chart of iron ore pellet plant process.md at main
Contribute to dihog/sbm development by creating an account on GitHub.
More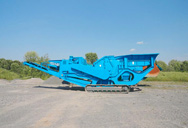
SINTERING AND PELLETISATION OF INDIAN IRON ORES
High grade iron ore less than 10% of the total reserves. ROM iron ore with Fe less than 58 – 60% discarded as waste. After beneficiation iron ore availability can improve by about 50%. Steel community and the country demand technological solutions for utilising low grade ores. The technology task that would be imperative: 1.
More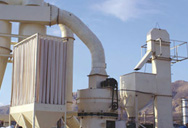
Our Businesses overview – EMIL
The IoBP plant comprises of a 1 MTPA Iron Ore Beneficiation plant and a 1 MTPA Iron Ore Pelletization plant based on first of its kind Circular Pelletization Technology (CPT) EMIL is also a pioneer in manufacturing of world class Noble Ferro Alloys (NFA) and Iron pellets. The Noble Ferro Alloys (NFA) unit is located in Valsad district of ...
More
Iron Ore Pelletizing Diagram - degraeflinsen
pelletizing plant process flow diagram. Iron Ore Pelletizing Process: An Overview IntechOpen. Jul 10, 2017 Figure 2 shows a flowchart of a typical pelletizing plant, highlighting the additive preparation, mixing and pelletizing feed preparation, the balling step, in this case using a disc pelletizer, and the induration step.
More
Chart For Processing Iron - degraeflinsen
Process flow chart of iron ore pelletizing industry. Pellet plant is facilitated with additives grinding unit as the process of pelletization requires binder and additives. Bentonite is used as a binder for proper balling of the filter cake particles in to spherical shaped balls with certain compression strength. The bentonite is stored and ...
More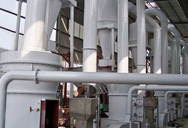
Iron Ore Pelletization: Part III. Organic Binders - Taylor Francis
2022年1月25日 This part reviews the goals of introducing organic binders into iron ore pelletization. Organic binders present a relatively small number of unique binding options but provide an extraordinary amount of flexibility in how to apply them. The key factors that lead into an effective organic binder are good dispersion into the iron ore, the ability ...
More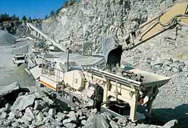
A review of binders in iron ore pelletization - Taylor Francis
2010年10月26日 The majority of iron ores must be ground to a fine particle size to allow the iron oxides they contain to be concentrated, and the concentrate must then be agglomerated back into large enough particles that they can be processed in blast furnaces.
More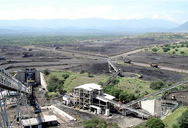
Minerals Free Full-Text A Comprehensive Recovery Process for ...
2022年3月19日 A comprehensive recovery process for the selective separation and enrichment of copper, zinc and iron minerals from a polymetallic ore was developed, which consisted of copper flotation, zinc flotation, and iron magnetic separation, and the adsorption mechanism of the copper collector Z-200 (O-isopropyl-N-ethyl
More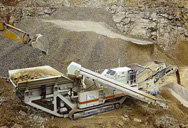
Pelletizing - an overview ScienceDirect Topics
2012年1月1日 The selection of an appropriate binder type and dosage is of critical importance in producing good quality pellets at a reasonable price. Binders accomplish two very important functions in iron ore pelletization: The binder makes the moist ore plastic, so that it will nucleate seeds that grow at a controlled rate into well-formed pellets.
More